Whatever the 3D print technique is, some kind of post-processing will be needed to make the part complete. Whether it be removing supports, using ultraviolet light to make a part strong, removing excess powder, or making a part smoother. I would like to review the optimal methods that MJF and SLS printing use to complete the Additive Manufacturing process. The methods (especially those automated) can increase productivity, create higher cost-efficiency, improve component performance, and faster implementation.
After the unpacking process, the first step in post-processing is CLEANING, removing the excess powder in MJF/SLS printing.
Media blasting systems need significant airflow to work properly to remove the unsintered loose powder, which can be accomplished with a sandblaster.
There is an extensive list of sandblasters that are on the market and these machines can be classified into four categories:
- Benchtop media blasters
- Floor top media blasters
- Tumbling blast cabinets
- SLS/MJF-specific depowdering blast cabinets
Benchtop blasters are recommended for users on a budget, typically with small to medium-sized print volumes and pricing up to around $1,000.
Floor top blasters are generally over $1,000 and offer a larger working space and are considered industrial quality.
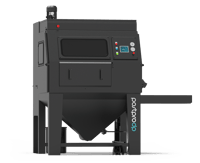
Tumbling blasters are an automated blasting process and contain a rotating drum with a blasting gun pointed at the SLS parts inside the drum. Parts are placed in the machine and left alone until the blasting cycle is complete.
SLS/MJF-specific media blasters exist at the same high-end spectrum as the tumble blasters. These are completely automated solutions for removing powder from parts, these blasters are more expensive but are market leaders for heavy SLS/MJF use cases. The cycle times are about 10 minutes to fully depowder parts.
Additional processing steps can be done beyond the media blasting process and some users may want to deploy vapor smoothing. Vapor smoothing is a finishing option for SLS/MJF/FDM printed parts that use vaporized chemical solvents to create shiny, smooth surfaces. Vapor smoothing can be used in various 3D printing technologies such as powder bed fusion, including SLS and MJF, as well as Fused Deposition Modelling (FDM). Vapor smoothing is a smoothed printed part that also retains its original mechanical properties.
Once parts are cleaned, users may want to change their color, two popular methods are spray painting and dyeing.
Steps for spray painting SLS/MJF parts are similar to that of other 3D printed parts. First, parts should be covered in multiple thin layers of primer. Then apply the spray paint to the surface of the part.
Dyeing parts can be done manually in an 80-100°C dye bath or an automated dying machine, such as Omegasonics 1818 Dye Tank which has a dual action high-velocity circulation system moving the heated dye material, through the SLS/MJF parts that might have hard to reach areas, blind holes, moving parts, hinges, and internal crevices, that can't be touched with paint. A lot of times, SLS/MJF parts are dyed and not painted because they can be complex geometries.
Traditional methods are slow, difficult to predict consistency, and can account for up to 60% of the part cost.
If you want to discuss a market leader, AMT Technologies, that offers automated post-processing solutions, please reach out to me via email at barbara.miller-webb@mastergraphics.com.